
Please take the time to read this before emailing and texting questions. Chances are, it’s all answered here for you. If you still have questions, give us a call or email. Thank you!
Please note any delays in delivery of packaging materials, faulty packaging materials, irregular packages (tall, slender, or tapered bottles), high filter pressures, filter changes, wine not at adequate temperature or other delays beyond the control of Ball Bottling, resulting in bottling delays or production will result in longer bottling times.
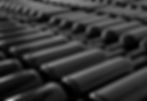
PRICING
$3000
Minimum daily rate
$500/ hour with a 6 hour minimum
Additional charges
Filter Cost : Market price
Filter Rental: $200 ( full price if filter is clogged)
Case Labels: .10cents per label
Generator Rental: $400/ day
Hotel Cost if needed
Travel fee where applicable
We can give you an estimate of how many days your job will take based of the information you provide. Depending on how many bottle changes, lot changes and case count will reflect the time it takes to complete each job. Based on packaging and speed of crew and client performance, we average on the low side 200 cases per hour and highs of 250 cases per hour.
If you want us to print case labels, we will need all information you would like on the labels one week prior to bottling to prepare them. These are standard 3x4 white labels and are still hand applied by your staff.
For those clients with multiple winemakers/clients in one bottling, it will be your responsibility to divide up the invoice at the end of bottling. Ball Bottling will create one invoice per job. Payment is due at the end of bottling and Ball Bottling accepts checks only.
Our pricing system is to help streamline billing and performance. It still breaks down as the same overall cost as previous pricing.
IMPRESSTIK VAC3001 LABELING MACHINE SPECIFICATIONS FOR BALL BOTTLING
Label Roll Diameter: 350MM Maximum
Label Placement: +/- 1mm per labeling head
Space between labels: Minimum 2.5mm / maximum 6 inches
Maximum label height: 180mm
Minimum label height: 6mm inch (confirm label by testing)
Maximum label length: 280mm
Minimum label length: 12mm (confirm label by testing)
Label roll core size: 3" I.D.
Label configuration: Fronts and backs alternating on a single roll
or
Liner types: Fronts and backs on separate rolls PET(clear)/44PK/Glassine / Kraft
Notes
-
Ball uses the Impresstik VAC3001 which has 2 labeling heads
-
Each labeling head will dispense either 1 label, or 2 labels with a space
-
Front and back labels are recommended on separate webs for tapered bottles
-
Consult Ball if your labels have unique attributes, such as being large, being small, odd shaped, multi paneled, clear materials etc. Some clear materials may need specific label gap sensors
